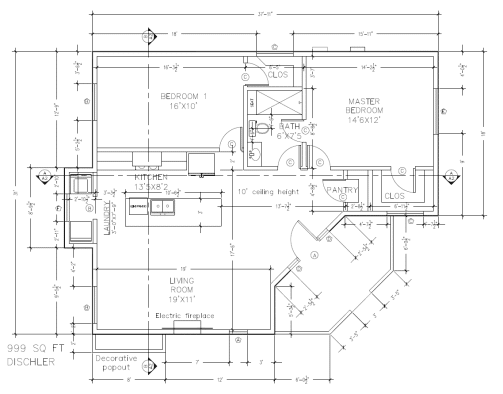
The Dischler Model
Our first project is titled Dischler. Dave, who has been my dentist for a few years now, was introduced to me by my wife, Valerie. She connected us because he’s someone who not only draws building permit plans but also handles construction. Dave and his family were looking to build a casita in their Scottsdale backyard for a relative. When I heard about this, I immediately thought it would be a great first project for OneSource. As always, we’re focused on building on a budget and doing so with an unconventional approach.
Our goal is to build using foam, but not the traditional SIP (Structural Insulated Panel) system, which uses wood sheathing on both sides. Instead, we’re promoting the GR Building System. This unique building system combines the strengths of structural panels and insulated concrete forms (ICFs) to create a sustainable building envelope. GR Building Systems, LLC has developed proprietary materials and techniques that set this system apart. Our building system has passed rigorous structural and environmental testing for code compliance, earning an Engineering Evaluation Report that approves our wall, floor, and roof systems. The system provides a fire-resistant, mold-resistant, and hurricane- and flood-resistant envelope that is up to 75% more energy-efficient than traditional housing. With the cost of wood framing rising, it’s time to consider alternatives that can save money.
I introduced the Dischlers to this new building approach, and while they were initially excited, they still preferred masonry because their main house is built with it. People often want new structures to match the existing ones. After discussing this, I began designing the casita. The first step was checking with the City of Scottsdale to confirm the requirements. I learned that the new building needed to be under 1,000 square feet. Working closely with the Dischlers, we created a plan that includes two bedrooms, one bathroom, a common kitchen/great room, and a small laundry room off the kitchen. The final plan was 999 square feet, fitting perfectly in a corner of the backyard with space for a driveway off the existing back RV gate.
When designing a new space, many people already have ideas based on their past experiences. The design process takes time to refine those ideas and make sure everything fits perfectly. For example, I thought a stackable washer/dryer would fit in one spot, but the Dischlers had other ideas. Having built other casitas before, they had specific preferences. They wanted the laundry area closer to the kitchen, so we designed a small pop-out room to fit a standard washer and dryer. This change allowed the space I had reserved for the washer/dryer to become a useful pantry instead.
Both bedrooms are spacious and feature walk-in closets. The bathroom is a ¾ bath, with a shower and two entry points—one from the master bedroom and the other for common access. Interestingly, Bedroom 1 is slightly larger than the master bedroom, primarily due to its location next to the kitchen. The shared wall allowed us to design a larger kitchen with ample cabinet space and a long island. I anticipate a single woman will be living here, so the extra bedroom can be used as storage, an office, or for whatever needs arise. As is common in modern homes, the kitchen and living areas are combined to create an open, welcoming great room.
Once I finished the design, I thought it could be a great addition to the OneSource house line. Currently, we offer three dwelling models: The Gibson, The Dischler, and The Duplexity. You can choose from one, two, or three-bedroom units. All models feature superior building materials, including 8-inch exterior walls, triple-pane windows, installed plumbing and electrical systems, your choice of a flat or pitched roof, stained or polished concrete floors, and 10-foot ceilings. We take pride in delivering a durable shell that will last a lifetime and beyond. This approach helps keep costs down, and another way to save is by helping with the construction. Like the Amish, working together and sharing knowledge can make the process more affordable and fulfilling.
As with any new design, there are challenges. Municipalities typically require a full set of plans, including a site plan that provides an overhead view of the proposed structure. This plan is essential for determining utility locations, property lines, setback lines, and other important details. New casitas usually need to be at least 5 feet from property lines and maintain a minimum distance from other structures.
One challenge I had to solve was how to add a new sewer line for the casita. The best solution is usually to run a line to the sewer main from the street, often connecting it to the main house. This may involve cutting through one or more concrete slabs to reach the front yard. If that’s not feasible, we might connect the new toilet to an existing bathroom inside the house.
For the front porch, the Dischlers wanted a covered area. Given the L-shaped roof design, we initially thought adding a cover would be tricky. I suggested they hire a metal fabricator once the permit is issued or, alternatively, buy a pre-made cover from Amazon.
Once the basic floor plan is complete, we move on to the elevations. These will show how the new dwelling will look, including window and door sizes. The Dischlers requested that the new casita match the existing house, so I incorporated similar rock work on the front elevation and chose a tile roof to match the main house.
Next comes the electrical plan, which includes placing ceiling fans, lights, and power outlets while ensuring compliance with building codes. We’ll also need to include panel schedules, load calculations, and one-line diagrams.
Beyond that, the remaining plans—such as the foundation, cross-sections, and construction details—are often overlooked by many, but they are critical for a successful build. Once all seven sheets are complete, we’ll hire a mechanical designer to create the heating and cooling plans. Recently, Scottsdale adopted the 2021 IRC building codes, which impose stricter requirements on mechanical and energy systems.
Once all the plans are submitted electronically, we’re ready to prepare a construction proposal. This aspect of the process is relatively new to me. As a designer, I’ve always focused on creating the plans, but I’m eager to expand my knowledge into the actual building process. One challenge I foresee is that traditional wood framing is still the norm, but we’re excited to offer an alternative that we believe will revolutionize how homes are built.